The Importance of Warehouse Safety: Key Practices to Ensure a Safe Workplace
- CI Group
- Oct 24, 2024
- 5 min read
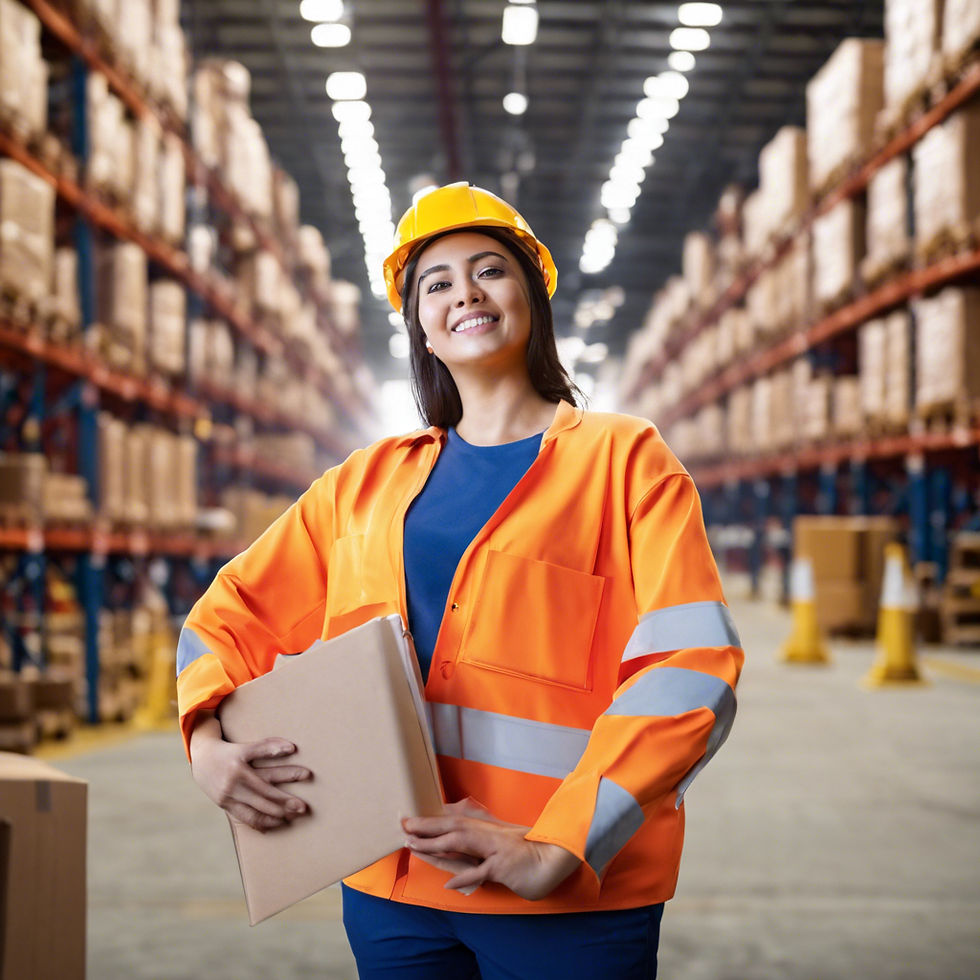
Warehouse safety is a critical issue for businesses in industries ranging from manufacturing and logistics to retail. With large amounts of stock being moved, stored, and accessed on a daily basis, warehouses can become hazardous environments if proper safety measures are not implemented. Unsafe practices can lead to accidents, injuries, and costly downtime, making warehouse safety an essential part of maintaining productivity, protecting employees, and ensuring regulatory compliance.
In this blog, we will explore the importance of warehouse safety and highlight key practices that can help minimize risks and create a safer work environment.
Why Warehouse Safety is Important
Preventing Accidents and Injuries Warehouses are filled with potential hazards such as heavy machinery, pallet racks, forklifts, and stored inventory. Without proper safety measures, accidents like slips, trips, falls, or collisions with forklifts can occur. Warehouse workers are also at risk of being struck by falling objects or getting injured while handling heavy loads. Implementing strict safety protocols helps prevent these types of injuries and ensures that employees can work in a safe environment.
Reducing Downtime and Increasing Productivity Accidents and injuries not only harm employees but also disrupt warehouse operations. When a workplace incident occurs, it can lead to delays, shutdowns, and loss of productivity as the affected areas are cleared, investigated, and repaired. By prioritizing safety, businesses can reduce the likelihood of incidents, minimize downtime, and ensure that operations run smoothly.
Protecting Equipment and Inventory Mishandling of machinery or improper stacking of inventory can result in damage to expensive equipment and goods. For instance, a forklift collision can damage racks, shelving, or even cause a stock collapse. Warehouse safety protocols are essential to safeguard the facility’s infrastructure, equipment, and inventory, thereby reducing the risk of costly repairs and losses.
Ensuring Compliance with Regulations Many industries are subject to strict workplace safety regulations enforced by organizations such as OSHA (Occupational Safety and Health Administration). Non-compliance with safety standards can lead to hefty fines, legal liabilities, and damage to the company’s reputation. Regular safety checks, employee training, and the implementation of safety measures ensure that the warehouse meets legal requirements and maintains a compliant, risk-free environment.
Promoting Employee Morale and Retention Employees who feel safe and secure in their workplace are more likely to be engaged, motivated, and productive. A strong culture of safety not only reduces injuries but also boosts employee morale and fosters a sense of trust. When workers know that their employer cares about their well-being, they are more likely to stay with the company for the long term.
Key Warehouse Safety Practices
To maintain a safe warehouse environment, it is essential to implement specific safety protocols and practices. Below are some key measures to prioritize:
1. Proper Training and Education
Employee Training: Ensuring that all employees are properly trained in the operation of warehouse machinery and equipment is critical to maintaining safety. Forklift operators, for example, should be certified, and all staff members should be educated on proper lifting techniques, handling procedures, and emergency protocols.
Safety Drills: Conducting regular safety drills can help employees stay prepared for emergencies, such as fires or equipment malfunctions. These drills ensure that workers know how to respond quickly and safely in hazardous situations.
Ongoing Education: Safety training should be continuous. As new equipment, protocols, or regulations are introduced, employees should be updated on the latest safety procedures. Regular refresher courses can also help reinforce best practices.
2. Clear and Organized Workspaces
Aisle Management: Warehouse aisles should be kept clean, clear, and free of clutter. Proper aisle management ensures that employees have ample space to move goods safely without the risk of tripping or colliding with machinery. Maintaining wide, organized aisles also prevents accidents involving forklifts and other vehicles.
Housekeeping: Spills, loose materials, and debris on warehouse floors can lead to slips and falls. Regular housekeeping and cleaning schedules should be implemented to keep the warehouse tidy and hazard-free. Employees should be encouraged to clean up spills and remove obstructions immediately when they occur.
3. Use of Personal Protective Equipment (PPE)
Proper Gear: Warehouse workers must wear the appropriate personal protective equipment (PPE), including hard hats, steel-toe boots, gloves, and safety goggles, depending on their specific duties. PPE minimizes the risk of injury when handling heavy loads, operating machinery, or working in high-traffic areas.
Enforcing PPE Policies: To ensure that all employees are wearing the proper protective gear, businesses should enforce strict PPE policies. Signage and reminders placed throughout the warehouse can encourage compliance, and supervisors should regularly check that employees are adhering to safety rules.
4. Safe Equipment Operation
Forklift Safety: Forklifts are one of the most commonly used pieces of equipment in warehouses, and they are also one of the most dangerous if not used properly. Operators should be certified, follow speed limits, use caution when navigating aisles, and inspect forklifts regularly to ensure they are in good working condition.
Routine Equipment Inspections: All warehouse equipment, including conveyor belts, pallet jacks, and loading docks, should undergo routine inspections to identify and repair any malfunctions or wear and tear. Preventive maintenance schedules help ensure that equipment operates safely and reduces the risk of mechanical failures that could lead to accidents.
5. Proper Stacking and Storage
Safe Stacking Practices: Poorly stacked goods can fall, creating a serious hazard for workers. Inventory should be stacked securely and at safe heights to prevent it from toppling over. Heavier items should be placed on lower shelves, and lighter items on higher shelves to maintain balance.
Rack Safety: Warehouse racks should be regularly inspected to ensure they are structurally sound. Any racks that are damaged or overloaded should be repaired or reinforced immediately. Signage indicating maximum load capacities can also help prevent overloading.
6. Clear Signage and Communication
Safety Signage: Clearly marked signs should be placed throughout the warehouse to indicate potential hazards, such as forklift traffic areas, emergency exits, fire extinguishers, and hazardous material storage. These signs should be visible and easy to understand to ensure employees are aware of the risks around them.
Communication Systems: Open and transparent communication is key to warehouse safety. Employees should be encouraged to report hazards, and a clear system should be in place for addressing safety concerns promptly. Regular safety meetings can help keep the team informed of any updates or issues.
Conclusion
Warehouse safety is an ongoing responsibility that requires commitment, education, and the proper implementation of safety measures. From employee training and equipment inspections to safe stacking practices and clear communication, a comprehensive approach to safety helps prevent accidents, protect employees, and maintain efficient warehouse operations.
Prioritizing warehouse safety not only reduces injuries and downtime but also creates a positive work environment where employees feel valued and protected. With the right protocols in place, businesses can ensure that their warehouses operate smoothly while keeping the safety and well-being of their workers at the forefront.
Комментарии